Beton jako materiał konstrukcyjny i wykończeniowy ścian oraz sufitów
W Polsce, szczególnie w przypadku budownictwa mieszkaniowego, jako wykończenie ścian i sufitów najczęściej stosowana jest warstwa tynku, którą się maluje. Dzieje się tak, ponieważ stosowanymi materiałami ściennymi są głównie pustaki ceramiczne oraz bloczki z betonu komórkowego, a stropy wykonywane jako gęstożebrowe. Aby więc zakryć połączenia i nierówności powstałe podczas murowania ścianę trzeba otynkować i pomalować.
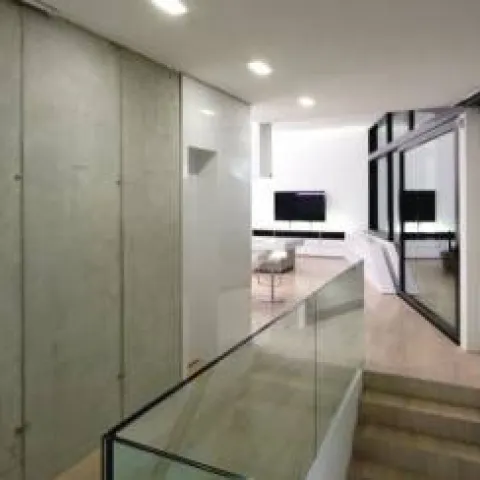
W budownictwie komercyjnym w przypadku szybów windowych i klatek schodowych, które najczęściej wylewane są z betonu towarowego zamiast tradycyjnego wykończenia ścian, pozostawiano surowy beton. Z jednej strony było to podyktowane chęcią obniżenia kosztów (eliminacja prac wykończeniowych), z drugiej pozwolił na to rozwój technologii betonu oraz jego wbudowania. Obecnie do wykonania tego typu konstrukcji stosuje się gotowe systemy szalunkowe umożliwiające wykonanie dobrej jakości powierzchni, narożników oraz połączeń elementów betonowych. Coraz częściej elementy betonowe: ściany, sufity stają się estetycznym wykończeniem wnętrza. Projektanci nowoczesnych obiektów sięgają po beton w celu podkreślenia charakteru pomieszczenia. Spotyka się różnego rodzaju wykończenia powierzchni betonu.
Aby z betonu wykorzystanego do wykonania ściany lub sufitu uzyskać atrakcyjną estetyczną powierzchnię należy:
- przygotować projekt zawierający rozwiązania umożliwiające uzyskanie oczekiwanego efektu
- zastosować odpowiedniej jakości szalunki
- wybrać wykonawcę, posiadającego odpowiednie umiejętności
- zapewnić, aby mieszanka betonowa była dobrze zaprojektowana
- zadbać, aby dobre warunki pogodowe sprzyjały wykonaniu elementów betonowych
- zapewnić odpowiednią pielęgnację betonu
Ważne jest, aby wszystkie z wymienionych elementów były spełnione. Często niedoświadczeni wykonawcy zaniedbują któryś z nich, co powoduje rozczarowanie.
Należy podkreślić, że mieszanka betonowa ma duży wpływ na efekt końcowy. Może ona zadanie ułatwić lub znacznie skomplikować. Po ułożeniu w szalunkach musi być dobrze zawibrowana. Jednak należy zwrócić uwagę, aby mieszanki nie przewibrować. Podczas wibrowania nie wolno dotykać elementów zbrojenia lub elementów szalunków, np. ściągów. Sposób układania mieszanki również ma duży wpływ na końcowy efekt. Ściany jako elementy cienkie bardzo często mają duże zagęszczenie zbrojenia. Znajdują się w nich, m.in. zbrojenie podłużne pionowe, zbrojenie rozdzielcze poziome. Zbrojenia te często wykonywane są jako siatki skręcane przy użyciu drutu wiązałkowego i układane przy obu powierzchniach ściany. Dodatkowo w szalunkach znajdują się dystanse. Wszystkie te elementy stanowią przeszkodę w układaniu mieszanki oraz stwarzają problemy podczas jej wibrowania.
Niestety projektanci nie zwracają uwagi na pewne detale, które ostatecznie mają duży wpływ na estetykę i projektują minimalne dopuszczalne przez normę grubości elementów, otuliny zbrojenia oraz odstępy między prętami. W związku z tym zastosowanie standardowych mieszanek betonowych nie jest korzystnym rozwiązaniem w tego typu elementach. Niestety bardzo często wykonawcy, optymalizując koszty budowy, „oszczędzają” na każdym elemencie składowym wykonania ściany. I daje to efekt opłakany.
Agilia Beton – dobre rozwiązanie do wykonania przegród pionowych i poziomych
Zastosowanie konstrukcyjnego betonu samozagęszczalnego Agilia Beton powoduje, że spora część wcześniej wymienionych zagrożeń zostaje wyeliminowana. Projektuje się go w klasie wytrzymałości C30/37, co obecnie jest odpowiednie do wylania konstrukcji nośnych w budynkach mieszkalnych i komercyjnych. Beton spełnia też odpowiednią klasę ekspozycji (od XC1 do XC4). Może być również stosowany w przypadku elementów zewnętrznych i wówczas spełnia klasę ekspozycji XF. Jeśli wymagana jest wyższa wytrzymałość betonu, może on być wyprodukowany w większej klasie.
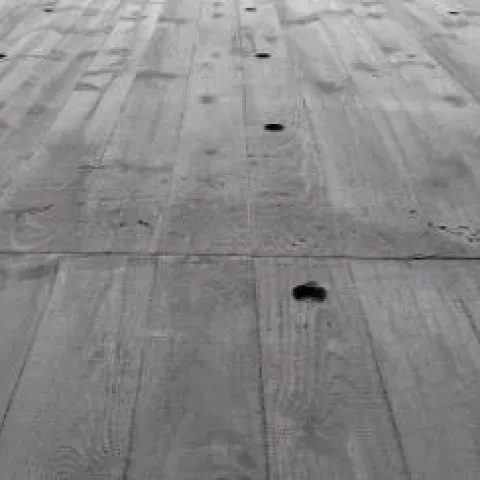
Spełniając oczekiwania konstrukcyjne Agilia Beton zapewnia wiele korzyści, ponieważ beton ten:
- jest samorozlewny – dzięki odpowiedniej kompozycji mieszanka płynie do 7 m od punktu wlewu, co pozwala na zmniejszenie liczby miejsc, w które wlewa się mieszankę w szalunek
- ma właściwości samopoziomujące – po wylaniu elementów poziomych górna ich płaszczyzna po przesztangowaniu charakteryzuje się dobrą równością, która eliminuje potrzebę stosowania wylewek wyrównawczych
- eliminuje potrzebę wibrowania – mieszanka betonu samozagęszczalnego nie powinna, a wręcz nie może być wibrowana, odpada więc czasochłonny, wymagający dużej uwagi i umiejętności oraz generujący wiele problemów proces wibrowania
- wypełnia równomiernie różnego kształtu szalunki – łatwo wylewa się elementy o skomplikowanych formach
- szczelnie wypełnia szalunki, dokładnie otulając zbrojenie – zmniejsza to ryzyko karbonatyzacji zbrojenia oraz wpływa na prawidłową współpracę zbrojenia z betonem
- umożliwia pompowanie od dołu – w przypadku wąskich i wysokich elementów konstrukcyjnych daje możliwość wlania mieszanki do szalunku bez obawy o zbyt dużą wysokość jej zrzucania
- bardzo dobrze odwzorowuje powierzchnię szalunku, w który jest wlewany – im lepszej jakości poszycie szalunku, tym dokładniejsza powierzchnia elementu, dzięki temu można również uzyskiwać różną fakturę powierzchni
Większość z wymienionych cech sprawia, że konstrukcyjny beton samozagęszczalny może być dobrym wyborem w przypadku potrzeby uzyskania dobrej jakości powierzchni betonowej ściany lub sufitu, gdy nie musi być to beton architektoniczny. Beton samozagęszczalny Agilia Beton zaprojektowany jest w dwóch podstawowych odmianach: do zastosowania w elementach pionowych (w tym w ścianach) oraz poziomych. Jest to związane z różnymi wymaganiami dotyczącymi wylewania betonu, rozkładu zbrojenia, grubości elementów. Uzyskanie różnej faktury powierzchni betonu możliwe jest przez zastosowanie specjalnych mat szalunkowych lub nabijanie na szalunek różnego rodzaju wykończenia.
Użycie betonu samozagęszczalnego Agilia Beton znacząco:
- upraszcza proces wylewania mieszanki do szalunku
- eliminuje proces wibrowania – nie ma potrzeby użycia, a nawet posiadania wibratorów
- zmniejsza liczebność ekipy niezbędnej do wykonania elementów
- zmniejsza czasochłonność
- zmniejsza zużycie energii potrzebnej do wylania elementu
- zmniejsza ślad węglowy elementów betonowych
- zapewnia bardzo dobrą jakość powierzchni elementów betonowych (w przypadku użycia odpowiedniej jakości poszycia szalunków)
- zwiększa wydajność ekipy budowlanej
W przypadku braku wykwalifikowanej kadry potrzebnej do wykonania dobrej jakości elementów betonowych oraz rosnących kosztów zatrudnienia, zastosowanie rozwiązań bądź produktów wpływających na usprawnienie pracy przy wykonywaniu elementów żelbetowych ma duże znaczenie. W przypadku, gdy te produkty dodatkowo poprawiają jakość końcowych elementów, to ich stosowanie jest szczególnie korzystne dla wszystkich uczestników procesu budowlanego.
Prefabrykowane ściany i stropy bez tynkowania i malowania
Wykonanie dobrej jakości elementów betonowych na budowie wciąż wiąże się z dużą niepewnością, dlatego coraz częściej wybierane są rozwiązania prefabrykowane. Wybór tej technologii może być podyktowany różnymi względami. Bardzo często jest to czas realizacji, uniezależnienie się od warunków pogodowych, wyeliminowanie wielu prac na budowie oraz jakość betonowych elementów prefabrykowanych, w tym powierzchni.
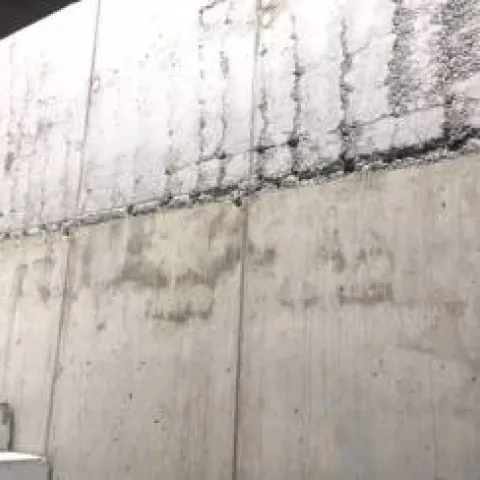
Inwestorzy, dokonując wyboru technologii betonowej prefabrykacji, mają świadomość, że odebrany element jest gotowy do wbudowania, charakteryzuje się odpowiednią wytrzymałością i stałością właściwości użytkowych. Wyprodukowane elementy prefabrykowane docierają na budowę zgodnie ze ściśle zaplanowanym harmonogramem, co w dużej mierze pozwala na ograniczenie do minimum wielkości placu budowy. Nie ma konieczności oczekiwania na odpowiednie warunki atmosferyczne czy uzyskanie wymaganej wytrzymałości przez młody beton, co znacząco skraca czas budowy.
Dodatkowo klienci najczęściej oczekują, iż dane zlecenie wykona jeden podmiot, co pozwoli zrezygnować z usług kilku podwykonawców i wyeliminuje problemy związane z komunikacją między różnymi firmami znajdującymi się na terenie budowy, a także uprości ścieżkę decyzyjną.
Przedsiębiorstwa produkujące prefabrykaty zatrudniają wykwalifikowaną kadrę specjalistów, którzy profesjonalnie doradzają na każdym etapie procesu budowlanego (od projektowania, przez wykonanie, transport i montaż na budowie gotowych elementów). Wiele z nich ma własne laboratoria, które na bieżąco kontrolują proces produkcji i odbiory elementów. Odpowiednie uzgodnienia dotyczące usytuowania instalacji oraz niezbędnego wyposażenia elementów pozwalają na zaprojektowanie prefabrykatów w sposób umożliwiający osiągnięcie maksimum korzyści z prefabrykacji.
W związku z tym, że prefabrykaty produkowane są z mieszanek betonowych, które mają dużą wczesną wytrzymałość, minimalna klasa betonu w przypadku elementów standardowych to najczęściej C30/37, a sprężonych C50/60. Elementy prefabrykowane wykonywane są w stabilnych warunkach oraz precyzyjnie kontrolowany jest proces pielęgnacji betonu, dlatego nie ma takich problemów z niedoskonałością powierzchni betonowej (np. rys w postaci drobnych siatek, tzw. pajączków), jak to ma miejsce w wielu przypadkach, gdy beton wylewany jest na budowie. Także dużo łatwiejszy jest do uzyskania jednolity kolor powierzchni.
Wytwórnia prefabrykatów ma ustabilizowany proces produkcji, powtarzalność surowców, stałą kontrolę przebiegu produkcji od przygotowania, wykonywania, transportu i odbioru elementów, co minimalizuje możliwość pomyłki. Produkcja elementów w wielkopowierzchniowych halach umożliwia uzyskanie dużej wydajności przy jednoczesnym zapewnieniu powtarzalności elementów. Większość producentów prefabrykatów ma własne wytwórnie betonu zlokalizowane bezpośrednio przy halach produkcyjnych, własne zaplecze laboratoryjne, zajmujące się zarówno projektowaniem betonów, jak i kontrolą jakości produkcji.
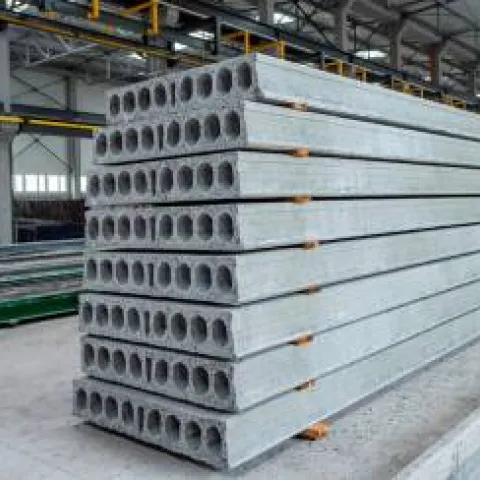
Do wykonywania stropów często wykorzystywane są sprężone płyty kanałowe np. HC – z angielskiego Hollow Core. Proces ich produkcji charakteryzuje się wysokim stopniem zautomatyzowania, a formowanie płyt za pomocą ekstrudera zapewnia uzyskanie gładkiej powierzchni dolnej. Powierzchnia górna płyty może mieć różną fakturę, w zależności od wymagań zamawiającego (zatarta na gładko, szczotkowana lub nawet zagrabiona w celu zwiększenia przyczepności do nadbetonu). Technologia pozwala na wykonanie dziennie kilkuset mkw. sprężonych płyt stropowych. Produkowane są one długimi pasmami o modularnej szerokości (najczęściej 1200 lub 2400 mm), a następnie cięte na wymaganą długość. Najczęściej mają wysokość: 150; 200; 220; 265; 320; 400; 500 mm.
Na budowie połączenia podłużne między płytami (nazywane pachwinami) zalewane są betonem. Czasami na płytach wylewany jest nadbeton (w zależności od wymagania projektu). Ważne, aby klasa wytrzymałości nadbetonu nie różniła się o więcej niż dwie od klasy betonu zastosowanego w płytach. Tak wykonany strop po zakotwieniu w wieńcu obwodowym stanowi płytę usztywniającą obiekt w poziomie.
Alternatywą do stropów monolitycznych są również stropy zespolone typu filigran, produkowane z betonu o wymaganej w przypadku konkretnego projektu klasie wytrzymałości oraz z odpowiednim zbrojeniem dolnym. Możliwa jest do uzyskania dowolna geometria i kształt. Dominują prostokąty z odpowiednimi otworami na instalacje. Prefabrykowane płyty o grubości 5 ÷ 7 cm i maksymalnej długości 8 m, usztywnione dźwigarkiem kratowym, mają szczególne zastosowanie w przypadku skomplikowanego kształtu stropu oraz dużej liczby otworowania. I
lość zbrojenia oraz parametry techniczne określa projekt wykonawczy opracowywany przez projektanta indywidualnie dla każdego obiektu. Powierzchnie dolne płyt prefabrykowanych, wykonywane na dobrej jakości łożach najczęściej są bardzo równe i gładkie. Dzięki temu sufit jest estetyczny i nie musi być tynkowany lub malowany. Takie rozwiązanie zaczyna dominować w budynkach biurowych lub użyteczności publicznej. Są też już pierwsze tego typu realizacje w budownictwie mieszkaniowym.
Jak wykonuje się ściany prefabrykowane
W przypadku ścian prefabrykowanych mogą być one wykonane jako: jednowarstwowe – składające się z warstwy nośnej, dwuwarstwowe – z warstwy nośnej i izolacji termicznej oraz trójwarstwowe – z warstwy nośnej, izolacji termicznej i elewacyjnej z betonu architektonicznego z fakturą lub zatartą na gładko. Najczęściej ściany produkuje się na stołach uchylnych posiadających osprzęt do formowania i zacierania zaformowanych powierzchni, czyli ściana produkowana jest na płasko, a następnie przez „uchylenie” ustawiana do pionu. W pionie się ją przechowuje, transportuje i montuje. W ścianach często zamontowane są już instalacje (elektryczne, wentylacyjne, teletechniczne, wodnokanalizacyjne). Wydajność procesu produkcji zależna jest od wielkości stołów, jakie ma producent i dziennie wynosi od kilkudziesięciu do kilkuset mkw. ścian.
Należy jeszcze raz podkreślić, że powierzchnie ścian prefabrykowanych w związku z wykonywaniem ich na stołach posiadających dobrej jakości poszycie charakteryzują się dużą gładkością i równością. Można je więc pozostawić bez dodatkowego wykończenia, co również wiąże się obniżeniem kosztów oraz zmniejszeniem czasu potrzebnego do wykonania gotowej ściany.
Elementy betonowe mogą być, a często już są stosowane jako estetyczne wykończenie budynku, szczególnie w przypadku ścian oraz sufitów. I taki efekt można uzyskać, stosując zarówno beton wylewany na budowie, jak i elementy prefabrykowane. Ważne jednak jest to, że gdy chce się otrzymać odpowiedni efekt, od samego początku należy pamiętać i uwzględniać to w procesie projektowania, następnie planowania i realizacji budowy. Tylko wówczas można spodziewać się oczekiwanego efektu w gotowym budynku.
Autorami tekstu są: Jędrzej Zdziechowski (Holcim Cement SA ) oraz Krystian Szczęsny (Zbych Pol & Mobet).